Zhengzhou Manxing Machinery Equipment Co., Ltd.
PRODUCT PARAMETERS
The MX101 Surface Integrated DTH Drill Rig is a cutting-edge drilling machine designed for surface mining, quarrying, and large-scale construction projects. It integrates a high-performance DTH drilling system with a screw air compressor, ensuring powerful, efficient, and precise drilling across various rock formations.
Description
1. Powerful Engine and Air Compression System
- Equipped with a high-power diesel engine delivering reliable performance for continuous operations.
- Integrated screw air compressor ensures optimal airflow for DTH hammer efficiency, reducing fuel consumption and enhancing productivity.
2. High-Efficiency DTH Drilling System
- Suitable for vertical, inclined, and horizontal drilling. Ideal for blast hole and pre-split drilling.
- Large-diameter hole capacity ranging from Φ90mm to Φ203mm.
- Delivers high impact energy for faster penetration rates, even in hard rock formations.
3. Advanced Hydraulic System
- Fully hydraulic control system for enhanced precision and safety.
- Independent hydraulic pumps ensure optimized power distribution for rotation, feed, and auxiliary functions.
- Eaton hydraulic motors extend service life with minimal maintenance.
4. Rugged Structural Design
- Reinforced steel feed beam designed for large-diameter holes, offering stability and efficiency.
- Caterpillar-style steel track chassis for superior stability and mobility on rough terrains.
- Hydraulic leveling jack legs ensure steady positioning during drilling operations.
5. Dust Suppression and Filtration
- Dual-stage air filtration system and a high-efficiency dust collector minimize airborne dust, improving safety and environmental protection.
- Large-capacity 14-core dust filters optimize dust removal performance in harsh environments.
6. Rotational and Feed Systems
- Heavy-duty rotary head powered by Eaton hydraulic motors with multi-bearing support for enhanced durability.
- Adjustable feed pressure and rotation speed for varying rock conditions.
7. Operator Safety and Comfort
- Ergonomic cabin design with air conditioning and noise reduction features.
- Centralized control panel for simplified and safe operations.
- Automatic rod handling system reduces manual labor and enhances productivity.
Applications
- Surface Mining: Ideal for blast hole drilling in open-pit mines.
- Quarrying: Effective for aggregate production and stone extraction.
- Construction Projects: Suitable for dam construction, foundation drilling, and tunneling.
- Geothermal and Water Well Drilling: Capable in deep, hard rock formations.
Product Advantages
Integrated Design: Combines drilling rig and air compressor in one compact unit.
High Efficiency: Fast penetration with powerful DTH drilling performance.
Heavy-Duty Construction: Built for extreme conditions.
Eco-Friendly: Advanced dust suppression and fuel-efficient components.
Operator-Centric: Safe and comfortable workspace with simplified controls.
Technical Specifications
Parameter | Value |
---|---|
Drilling Diameter | Φ90mm – Φ203mm |
Maximum Drilling Depth | 40 meters |
Engine Power | 180 kW Diesel Engine |
Compressor Capacity | 18 m³/min – 24 m³/min |
Compressor Pressure | 1.7 MPa – 2.4 MPa |
Feed Force | 25 kN |
Rotation Torque | 4500 N·m |
Track Chassis Type | Heavy-Duty Steel Tracks |
Climbing Ability | 25° |
Dust Collection System | 14-core dual-stage filter |
Machine Weight | 14,000 kg |
Transport Dimensions | 7500mm × 2300mm × 2900mm |
FAQs
- Applications: Designed for drilling water wells in various geological conditions (soft soil, sand, gravel, and hard rock).
- Features:
- Compatible with air compressors or mud pumps for efficient drilling in diverse terrains.
- High mobility with trailer/truck-mounted configurations for remote site access.
- Typical drilling depth: 100–500 meters, adaptable to regional requirements.
- Advantages: Energy-efficient, user-friendly controls, and modular design for easy maintenance.
- Applications: Geological exploration (metal/non-metal mineral surveys), hydrogeological studies, and oil/gas field exploration.
- Features:
- Rope coring technology for precise sample extraction.
- Hydraulic systems for stable operation in challenging environments.
- Drilling diameter: 50–150 mm; depth up to 1,000 meters.
- Advantages: High core recovery rate, low vibration, and compatibility with wireline drilling systems.
3. DTH (Down-the-Hole) Drilling Rig
- Applications: Ideal for hard rock formations in mining, quarrying, and geothermal projects.
- Features:
- Pneumatic hammer drills for rapid penetration.
- Adjustable air pressure (1.7–3.5 MPa) and customizable hole diameters (102–114 mm).
- Supports depths up to 300 meters.
- Advantages: Reduced deviation, high drilling speed, and minimal wear on tools.
4. HDD (Horizontal Directional Drilling) Rig
- Applications: Underground pipeline/utility installation without trenching, suitable for urban areas and river crossings.
- Features:
- GPS-guided steering systems for precision.
- Torque capacity: 10,000–30,000 Nm; pullback force up to 200 tons.
- Drilling length: 100–2,000 meters.
- Advantages: Environmentally friendly, minimal surface disruption, and adaptable to varying soil types.
5. Excavator Mounted Drilling Rig
- Applications:
Mining and Quarry Drilling:Efficient for blast hole drilling in open-pit mines, quarries, and aggregate extraction sites.
Slope Stabilization and Anchoring:Ideal for drilling anchor holes on slopes, embankments, and landslide-prone areas to install rock bolts and soil nails.
Foundation and Piling Work:Used for drilling foundation holes in urban construction, bridges, retaining walls, and infrastructure projects.
- Feature:Easily converts your excavator into a powerful and flexible drilling rig for rock, soil, and foundation applications.
Key Selling Points:
Compliance: Meets international standards (ISO, CE) and adapts to local regulations (e.g., EU VAT, environmental policies).
Customization: Tailored configurations (e.g., crawler/wheel-mounted) to meet project-specific needs .
After-Sales Support: 24/7 technical assistance, regional service centers, and extended warranty options .
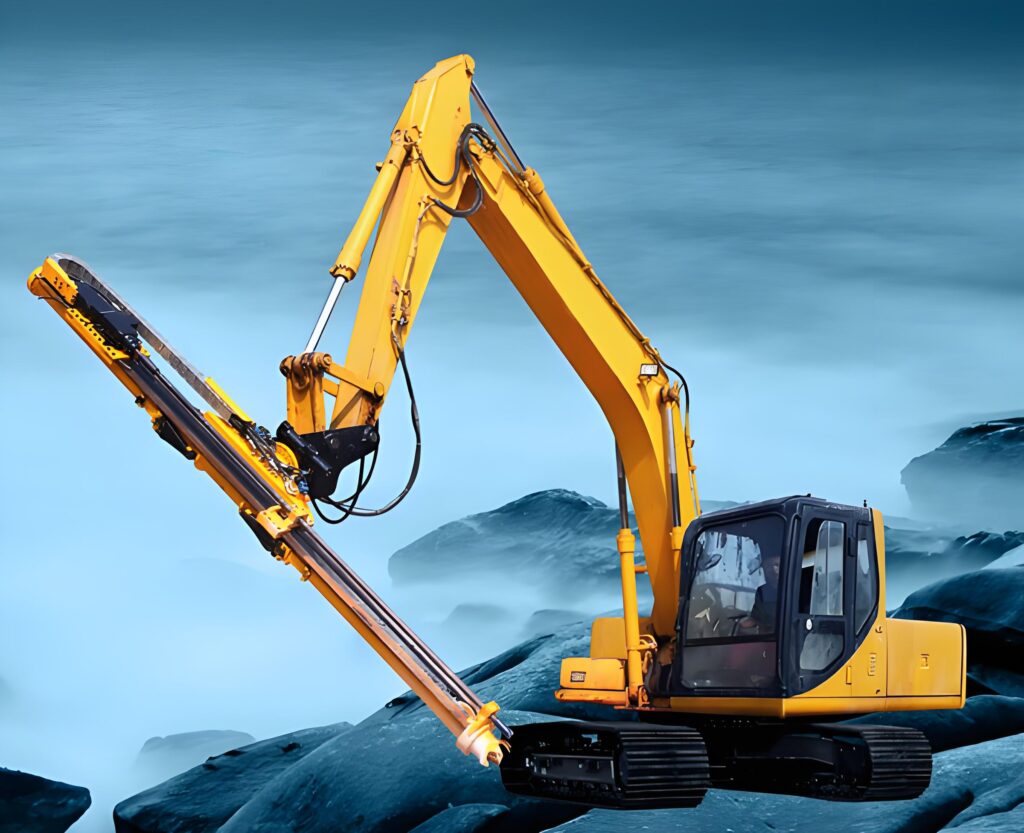
We offer high-efficiency logistics solutions and secure delivery of heavy-duty drilling equipment. Here’s how we handle shipments:
Support EXW, FOB, CIF, DDP, etc., tailored to your needs.
Transportation Options
Sea Freight: Cost-effective for large machines (e.g., rigs exceeding 10 tons). Suitable for long-distance international shipments. Delivery time: 25–45 days1.
Air Freight: Fast-track delivery for urgent orders or spare parts. Delivery time: 3–10 days1.
Land Freight: Ideal for regional deliveries (e.g., within Asia or Europe). Includes truck or rail transport.
Multimodal Solutions: Combined sea/air/land transport for optimized cost and efficiency.
Packaging & Safety
Heavy machinery is securely packed with steel frames, weatherproof wooden crates, and anti-rust treatments1.
Fragile components (e.g., hydraulic systems) are individually padded and labeled.
Customs & Documentation
We provide full export documentation (commercial invoice, packing list, COO, etc.) and assist with customs clearance globally.
Delivery Assurance
Real-time tracking: Monitor shipments via our logistics platform.
Insurance coverage: Optional all-risk insurance for high-value equipment.
Flexible Trade Terms
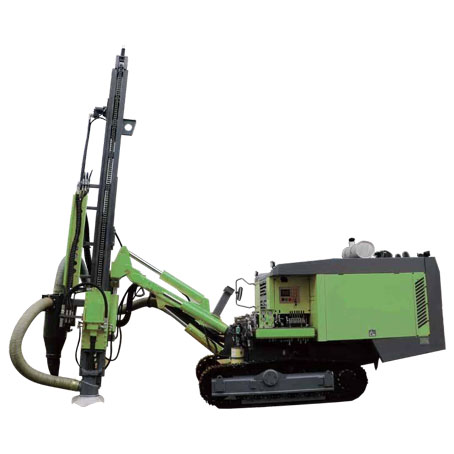
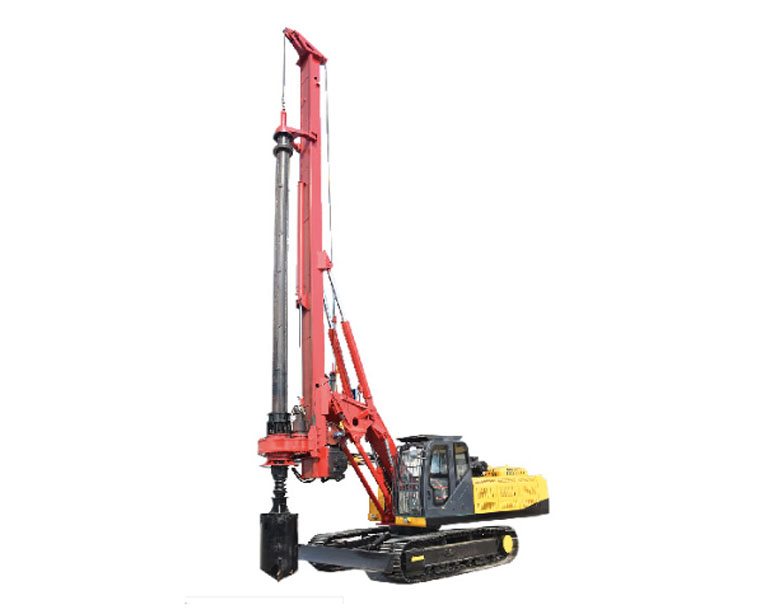
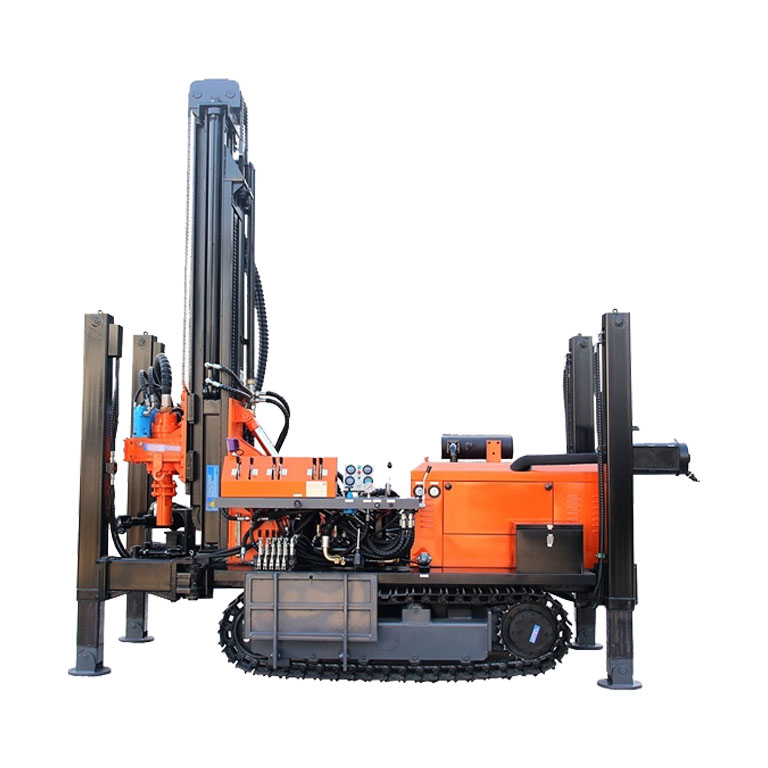

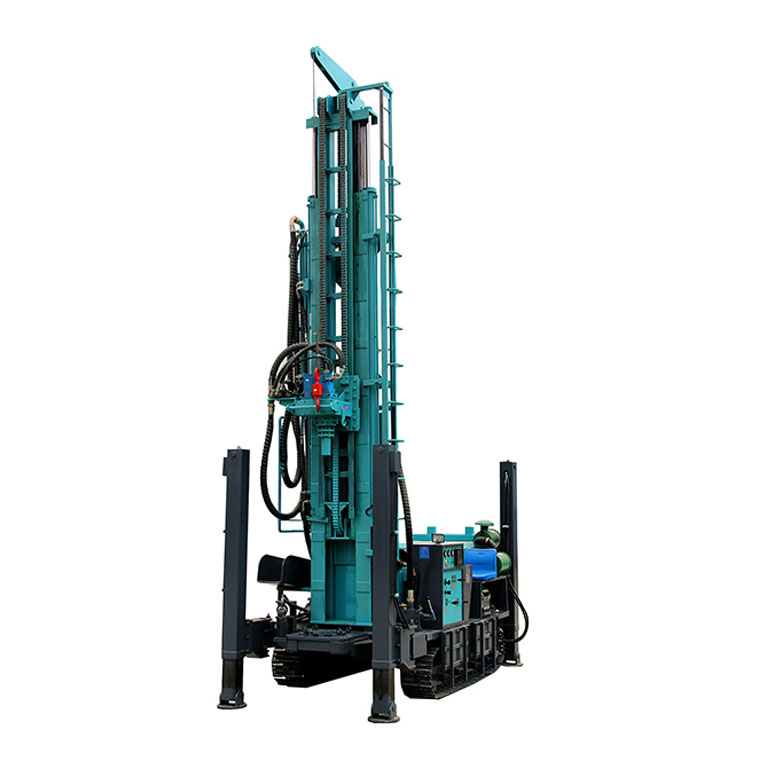
Yes, mechanical equipment can be fully customized to meet your specific requirements. Here’s a structured overview:
1. Customization Scope
- Functional Adaptations: Tailored to your operational needs (e.g., power output, precision, automation level) .
- Design Modifications: Adjustments in size, material, and ergonomic layout to fit your workspace.
- Integration Capabilities: Compatibility with existing systems (e.g., IoT sensors, production line interfaces).
2. Key Benefits
- Optimized Efficiency: Custom designs align with your workflow, reducing downtime and energy waste.
- Cost Savings: Eliminate unnecessary features while prioritizing critical functionalities.
- Competitive Edge: Unique equipment enhances product quality and differentiation in your market.
3. Process Overview
- Consultation: Detailed analysis of your needs and operational environment.
- Prototyping: 3D modeling and testing to validate design feasibility.
- Production: Advanced manufacturing techniques (e.g., CNC machining, laser cutting) ensure precision.
- Post-Sale Support: Installation, training, and maintenance services included.
4. Industries Served
- Heavy machinery, automotive, aerospace, and precision engineering sectors.
For a tailored solution, collaborate with a specialized manufacturer to discuss technical specifications and project timelines. Let us know your requirements—we’ll handle the rest!